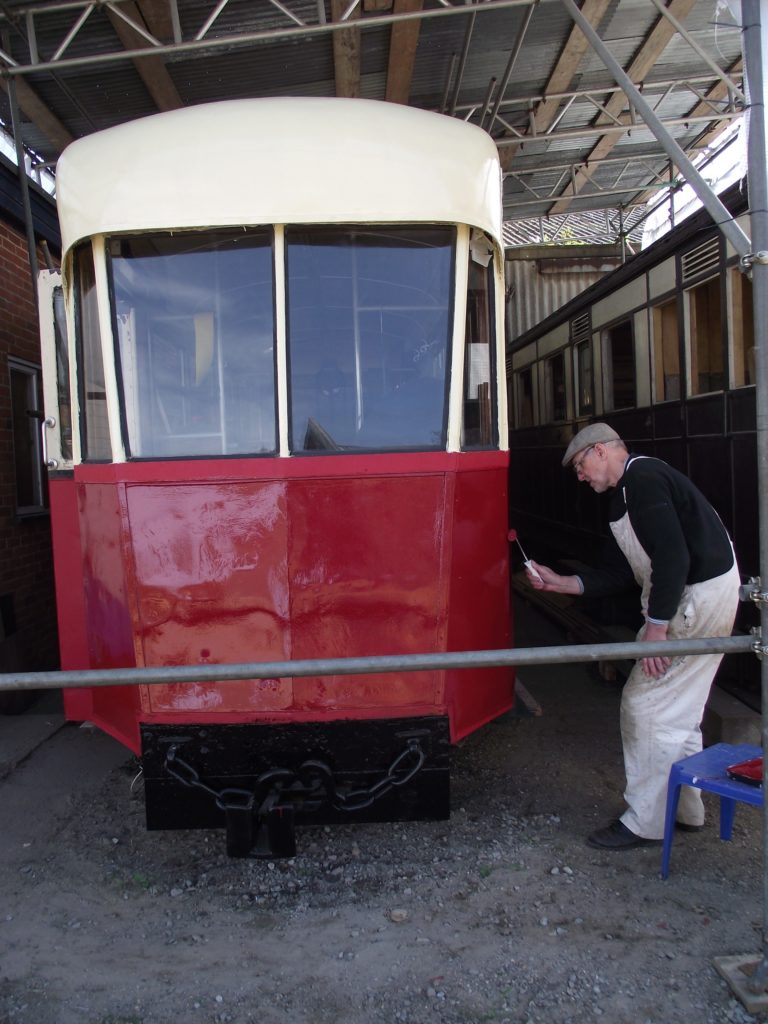
A number of scheduled workparties, and one or two extra days, have really started to show results with coach 7 and the wagon underframe. Panelling for the coach Southwold end is measured for order, a great deal of finicky work on the inside of the doors – framing, panelling and aluminium sheet – is well in hand.
The doors are awkward to access, as they concertina open and closed in the step wells – when open, the leaves are back to back (and therefore can’t be got at), and when closed, the leaves are up against the step risers. Regular worker Toby patiently gets on with it (even when another volunteer opens a door which he has just glued, mended and clamped, thus removing all the clamps). As a bit of light relief, he is also building a small bar in the corner a la Titfield Thunderbolt, where we can put our cups of tea (and perhaps other liquids, later).
The entire roof and upper body sections are now complete and in gloss regency cream, apart from a couple of tweaks on some broken aluminium moulding; both headstocks will soon also be complete in black gloss, and we have made a start on the maroon gloss lower body panels. This is a much more railway-like colour than it looks in the photos, being, basically, Midland Red.
Although there’s still the panelling and trim to complete in both ends, and the ceiling in one end, the end is in sight for this phase: the underframe and brake system will follow.
The onerous task of drilling a hundred or so holes in the wagon steel underframe continues: one headstock timber cover is done, and the plates (which support the body) marked out against the solebars. The picture shows the solebars in situ, awaiting brackets and bolts, and the plates (not yet cut to length) on the top of the underframe. The coach bolts to fix the coupling drawgear timber “washers” had to be modified (well – ground down by hand, really), as the original fittings were rebated into the countersunk metal completely, presenting a flat surface looking like a flush rivet. These we could not source, so hence a lot of grinding. In fact, one of the coach bolt heads was ground a bit too far, and when the nut was tightened, the entire bolt proceeded to fold up its remains of a head and pull through the hole. One lives and learns.
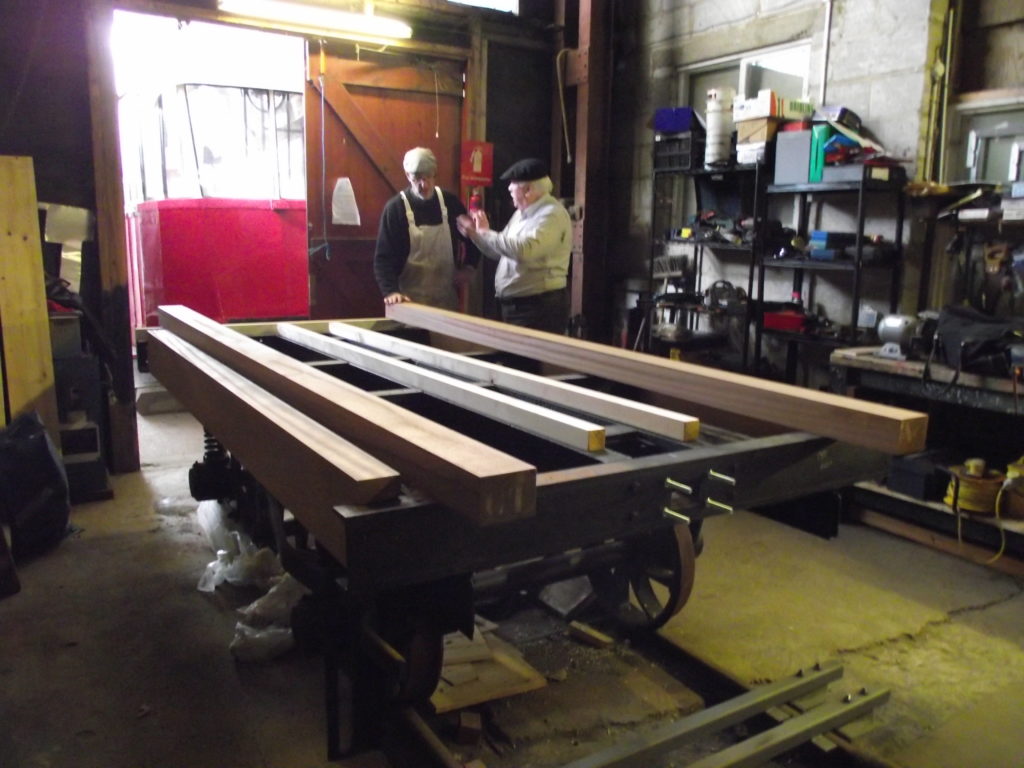
Two of the rails recently collected have been cut to length, drilled
for fishplates (very nice new ones from GB Rail), and also drilled at
24” intervals for the M12 studding which holds them to gauge. One of the
rails turned out to have annealed (or perhaps been in a bonfire), as it
blunted three or four very expensive hole cutters, and seven or eight
high-quality drill bits. When you have already blunted a number of bits,
using proper cutting fluid, and the 13mm (or 19mm) diameter hole is
still a shallow depression about 2mm deep – you begin to wonder about
the resilience of some materials.
The track panel – of about 10 feet – will be plated onto the existing
panel under the coach underframe, so we can safely attempt to roll it,
to see whether it does in fact roll, and if so, what condition the
wheels, suspension and axleboxes are in.